Our approach Expert service for first-class performance
End-to-end support
Over 300 employees are on hand to advise you at all stages of the acquisition of an aerial work platform. Each stage is different and important : research, design, manufacturing, assembly, testing, delivery, and commissioning, training and on-site maintenance are managed by France Elévateur working at your side.
This extensive support allows us to control the entire chain.
Our approach
Your commercial contact masters the process perfectly and ensures the definition of your needs as well as its follow-up from manufacturing to delivery.
Contact us1 - Research
Our design office that consists out of a team of 25 specialists, including two who have their PhDs in engineering, is eager to learn your needs and implement them. A thorough market analysis is also required in order to design the aerial work platform of tomorrow.
A significant part of the budget of our research department and engineering office is allocated to R&D, whose work has been rewarded through the registration of numerous patents.
2 - Design
Our design office is segmented into different categories, mechanics, hydraulics and electronics. Each category is represented by a team leader that is responsible within his domain for their specific contribution, whether it has to do with the structure, the controls or the energy-management components.
3 - Assembly
The assembly of the machines is done in our plant in Flavigny-sur-Moselle and each production section is managed by a dedicated team. We prioritise French-made products and short supply chains as much as possible. Therefore, for example, our booms are fully assembled in our factory.
4 - Training
Our training department “FE TRAINING” offers a range of training courses related to the operation of our machines. They are designed, not just for end users, but also for fleet managers:
– Maintenance training
– Licence to use height-access equipment (PAL by IPAF)
– Refresher course in the use of emergency manoeuvres
5 - Support
11 after-sales agencies, staffed by more than 80 people and equipped with 20 call-out vehicles, cover the French territory, with a set-up that allows our customers to be within 200km of technical support in less than two hours. They ensure conventional maintenances, repairs, compulsory biannual control for the lifting machines.
Our distributors ABC EQUIPEMENT, based in Reunion Island, and POLY DIESEL in French Polynesia have been providing the same quality service for more than 20 years.
Quality, one step closer to excellence!
Our customers' requirements are constantly changing. Therefore, in order to always respond positively to this change and to maintain its image as a major player in the design and manufacture of aerial work platforms, France Elévateur must continually improve the quality level of its products and services.
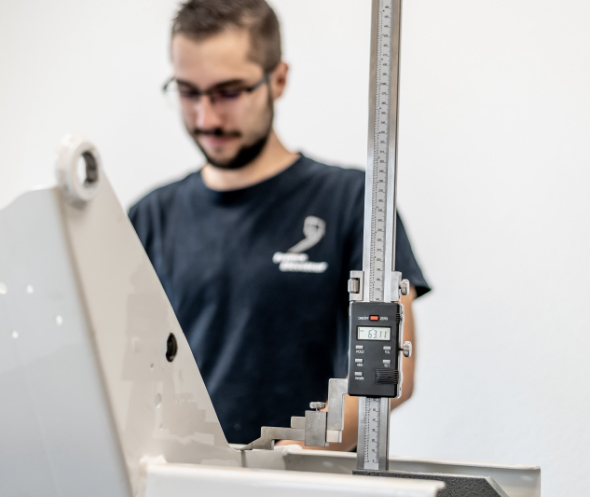
Our suppliers, therefore, are part of a continuous improvement process that aims to supply products that comply 100% with requirements.
France Elévateur provides quality in all processes, from the receipt of its components to the delivery of the finished product.
Before each delivery, all our machines are weighed and undergo static and dynamic operating tests combined with more than a hundred control points, guaranteeing our customers a vehicle that complies in all respects with their expectations and with regulations.
Certified to the latest version of the international quality standard ISO 9001, France Elévateur decided to extend this certification in 2021 to all its after-sales service network, demonstrating its commitment to service and customer satisfaction.
As the safety of our machines depend on the assembly of our booms, France Elévateur has chosen to keep this activity indoors, which is a genuine asset and an example of French know-how.
Our quality controllers believe that the quality of today is not sufficient for that of tomorrow! The quality control department doubled its workforce in 2019.
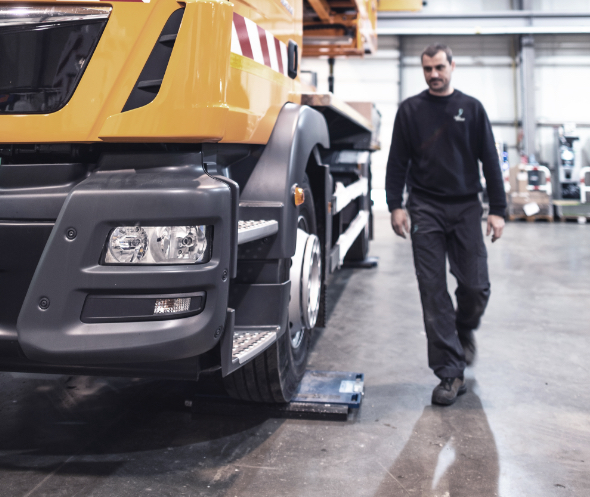